- Overview
- Detailed Photos
- Our Advantages
- Brand List
- Features and Configuration
- Peripheral Equipment
- Product Parameters
- Packaging & Shipping
- Products Application
Basic Info.
Product Description

GUANGDONG SHIMI INTELLIGENT EQUIPMENT CO.,LTD
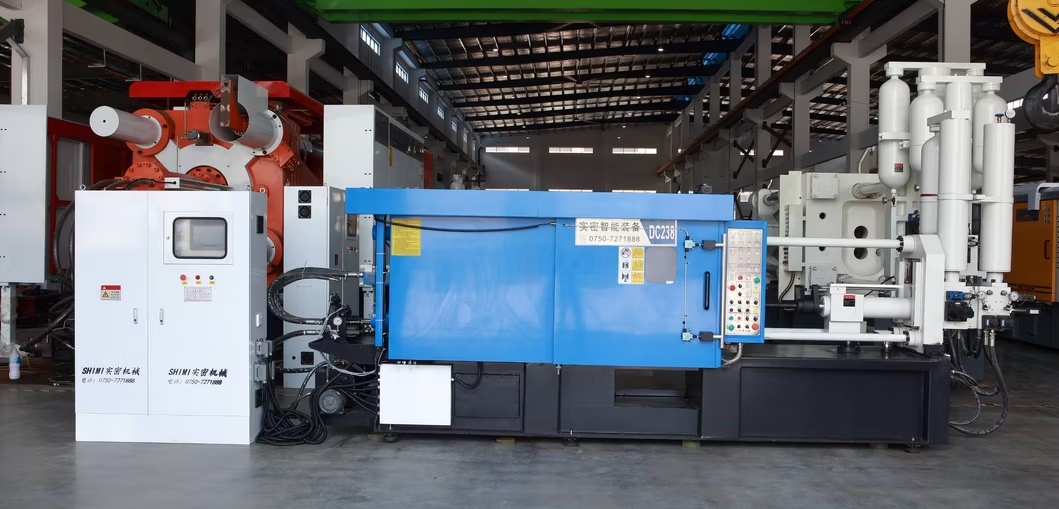
Aluminum Die Casting Machine with Servo Motor DC 238Ton Cold Chamber Machine
The servo energy saving system can be applied to all models of Shimi die casting machines. Cold chamber die casting machine and hot chamber die casting machine.
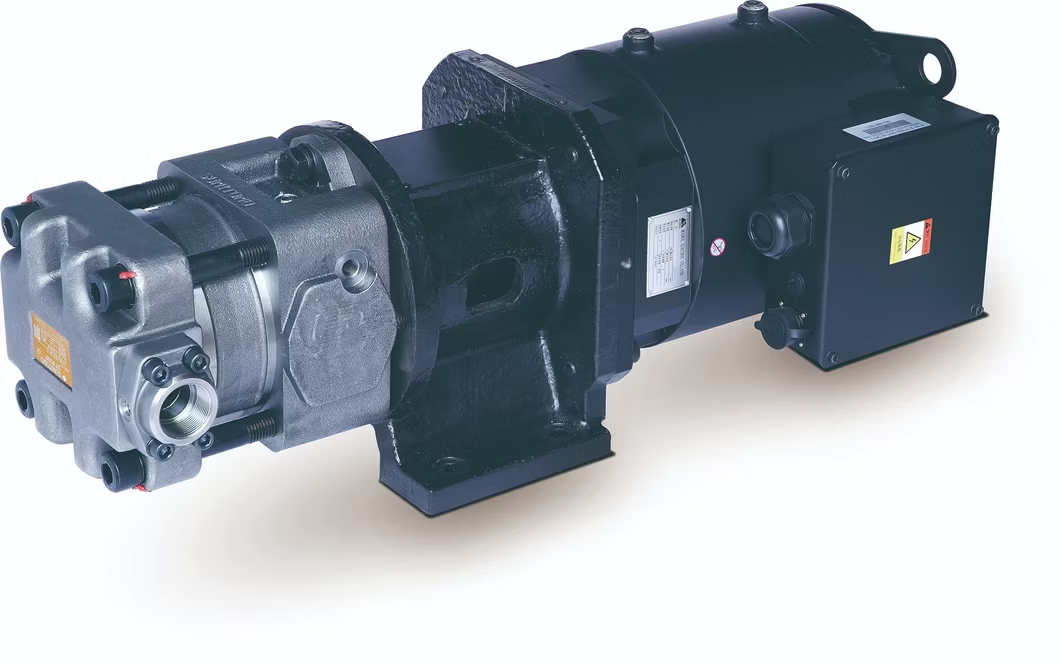
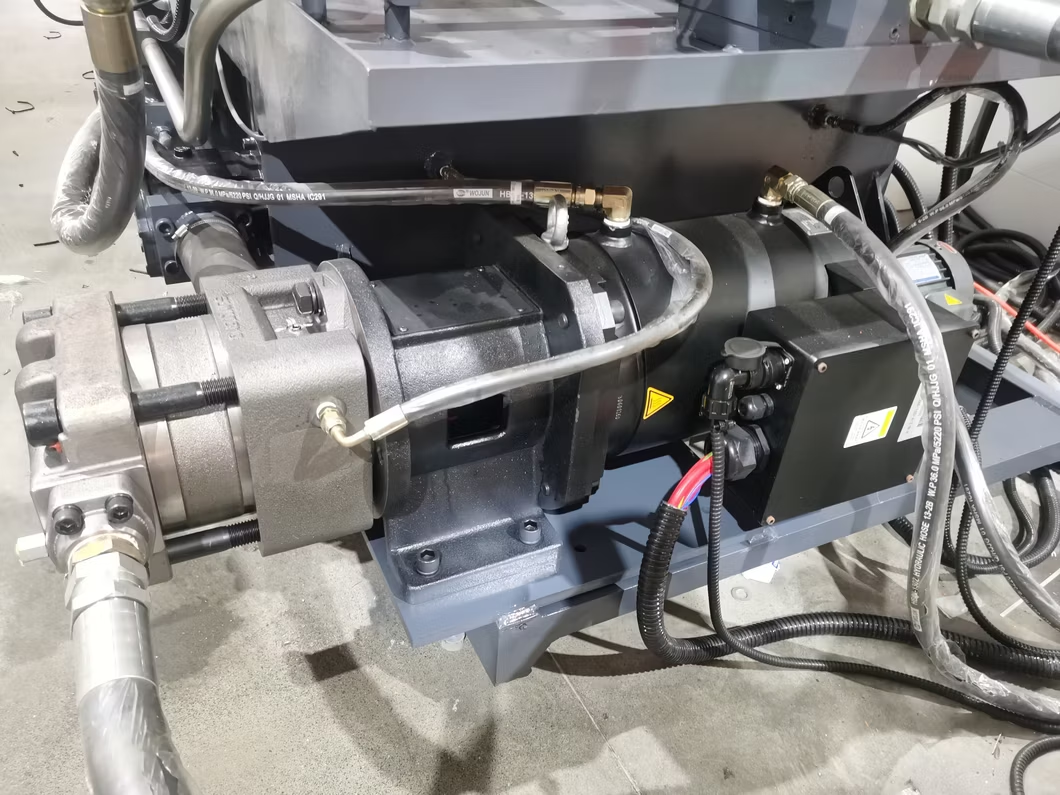
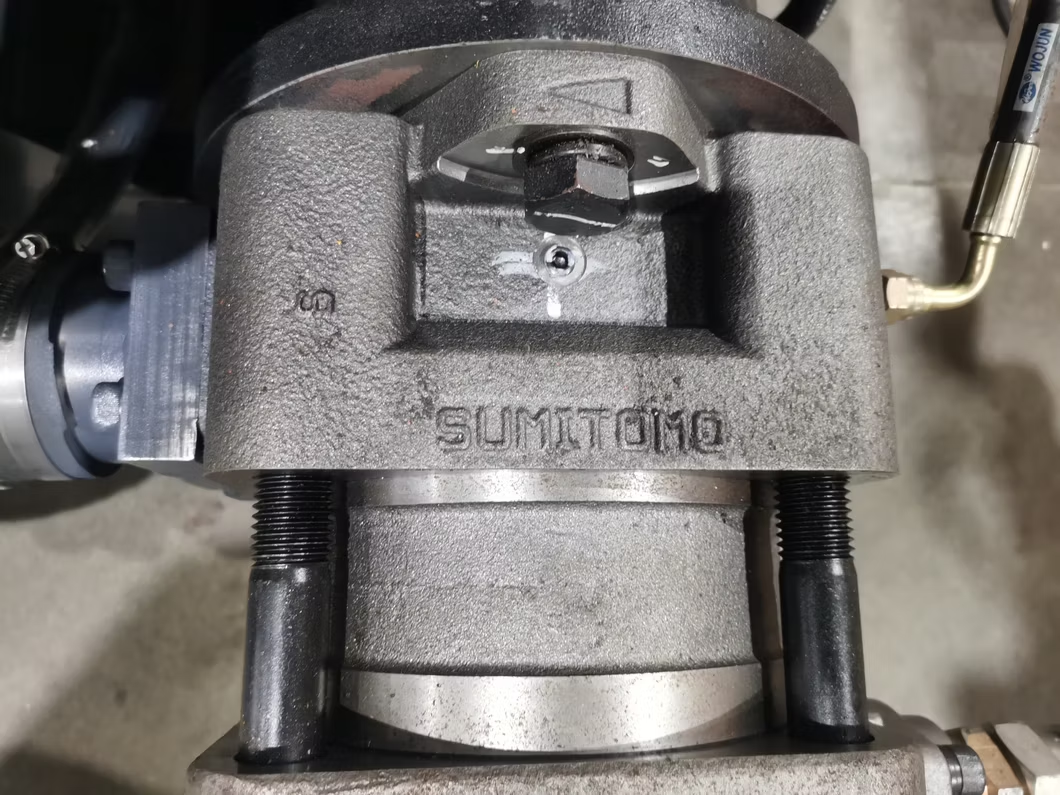
The servo energy saving system can be applied to all models of Shimi die casting machines. Cold chamber die casting machine and hot chamber die casting machine.
The die-casting machine automatically adjusts the flow rate and pressure according to the computer setting, and the overall energy-saving effect can reach 45%~75%.
Low noise, < 65dB during normal operation, to achieve quiet operation and improve the working environment.
The dynamic response time of the whole system is < 50ms, and the production efficiency is increased by more than 5%~7% compared with ordinary models.
The PID adjustment of the flow rate and pressure of the oil-cooled servo drive makes the repeatability of the entire oil circuit system controlled within 0.3% to ensure product quality.
The double closed loop of flow and pressure is adopted to make the machine run smoothly and repeatedly, greatly reduce the impact, reduce the wear of each component, and prolong the service life.
- Siemens PLC Controller
- Siemens 7" or 10" touch screen
- Air Switch, button Switch and AC Contactor are Schneid
- Hydraulic Valves are Yukan Japan
- Servo Motor: Modrol, China
- Servo Pump: Sumitomo, Japan
- Lubricate oil pump: Herg, Sino-Japanese joint venture
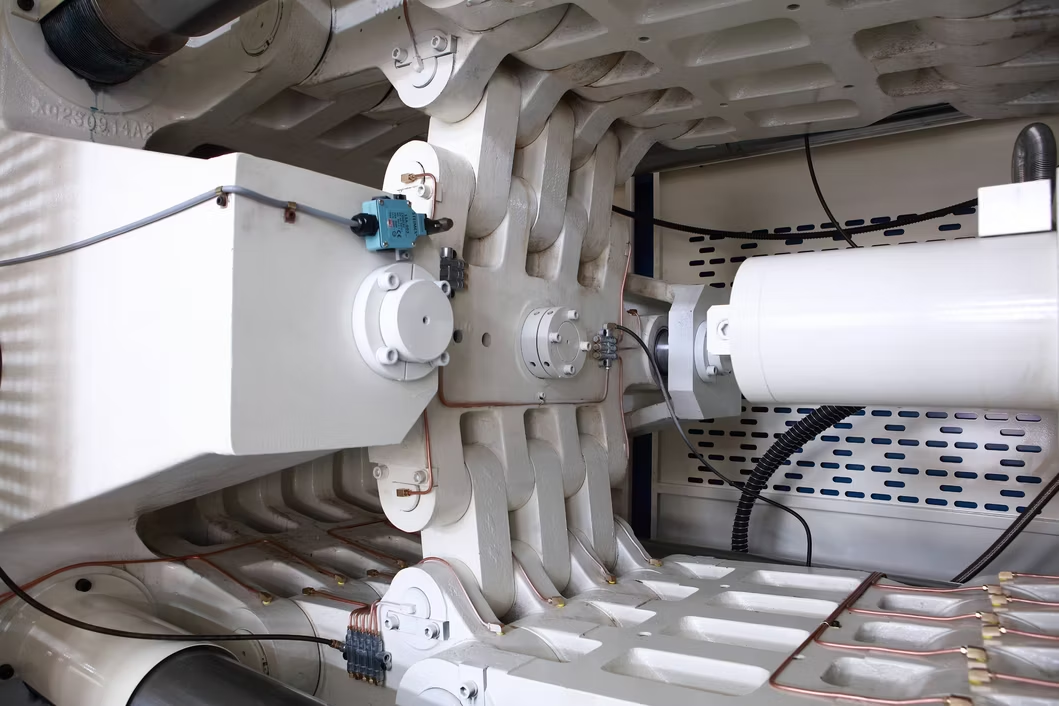
Mold clamping unit adopts Five-dot type toggle design, which optimized structure of connecting road and enhanced sports properties.
The steel bushing of hinge pin adopts alloy steel bushing (oil lubrication exist simultaneously),which reduce times of lubrication and prevent locking of toggle when no oil .
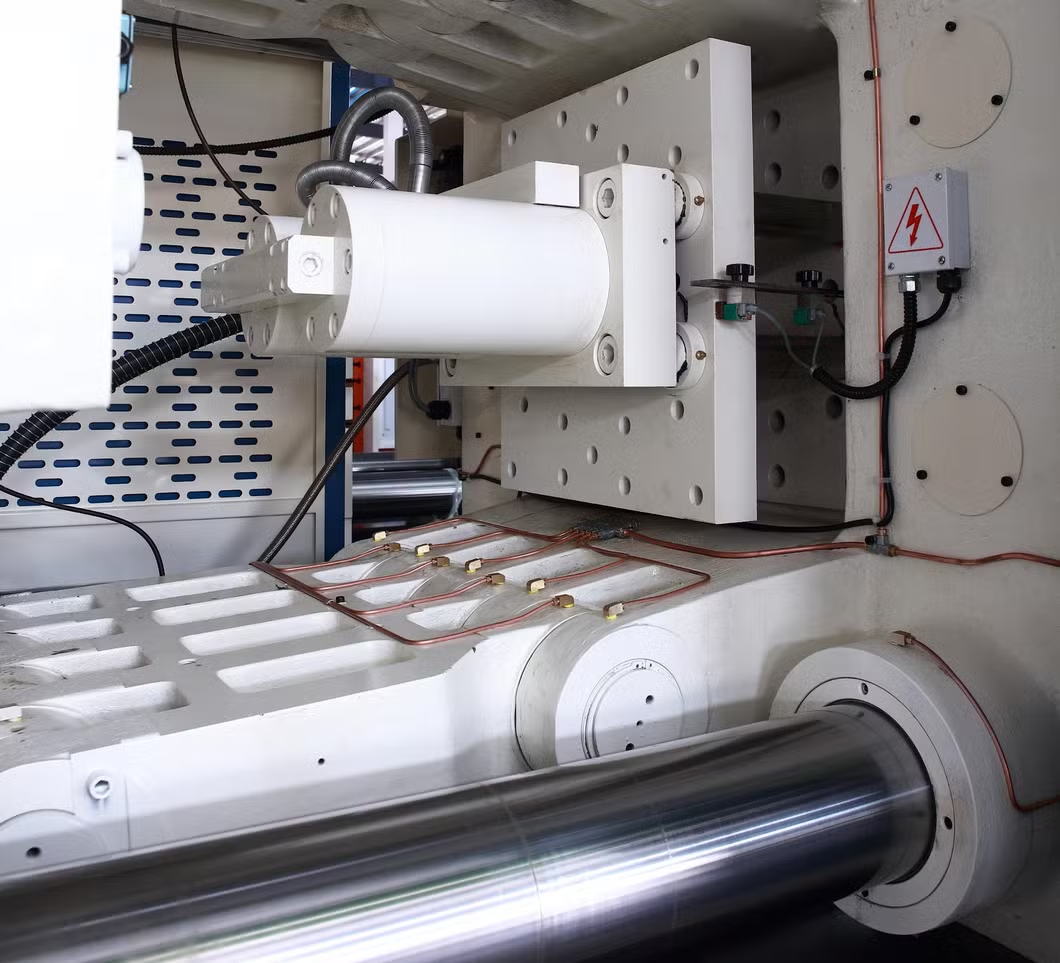
The optimization design of die platens have been carried out multiple times through analysis of element software, then strengthening design (increased thickness and support ribs of castings ), which both guarantee the service life of die platen and mold. The tie rods of each machine have passed the test by professional testing organization, to ensure the deflection of tie rod within reasonable scope during the operation of machine.
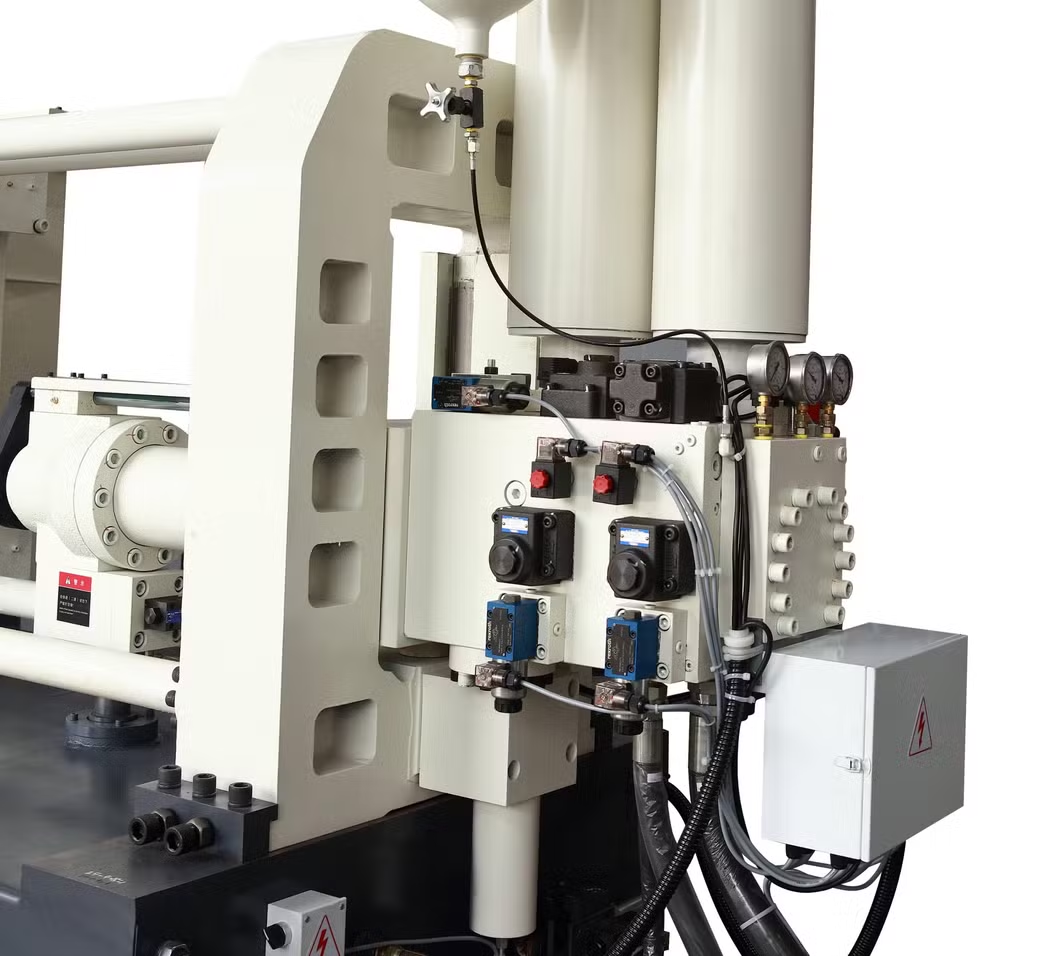
Using 17.5Mpa system pressure, the maximum dry shot speed reaches to 8-9.5m/s, the injection force increases about 5-8%, it is more easier to molding to products with thin wall or high requirement on air tightness and surface finish, to reduce porosity of die castings effectively , especially suitable for automotive castings and stress castings.
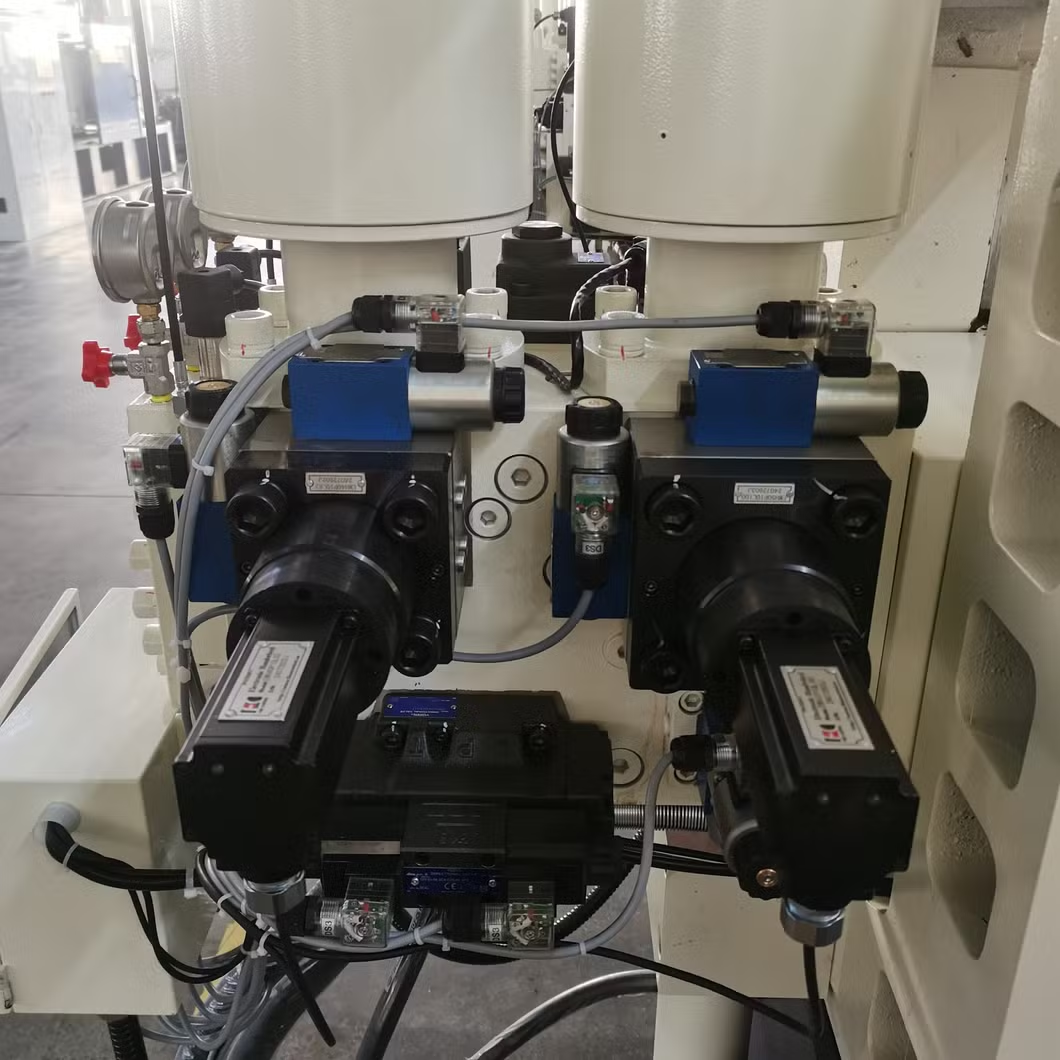
The electric control valve achieves higher precision in injection speed control.
Convenient and labor-saving adjustment .
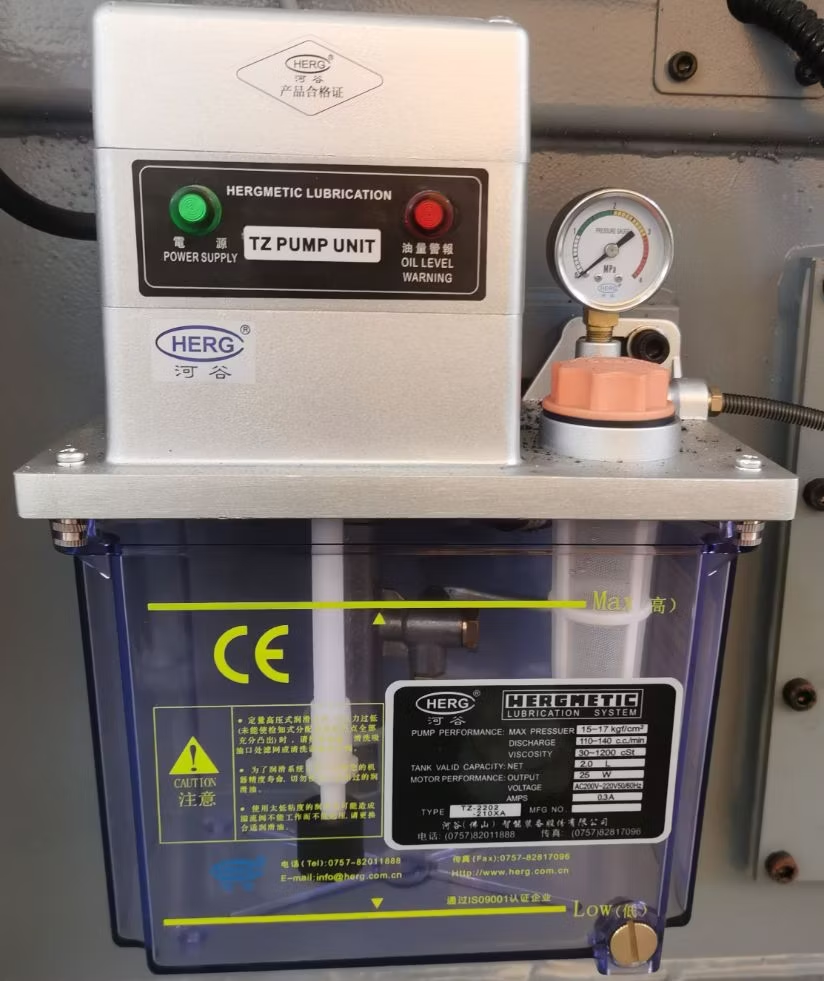
Central automatic lubrication system, timing lubrication toggle to improve mechanical life and reduce maintenance.
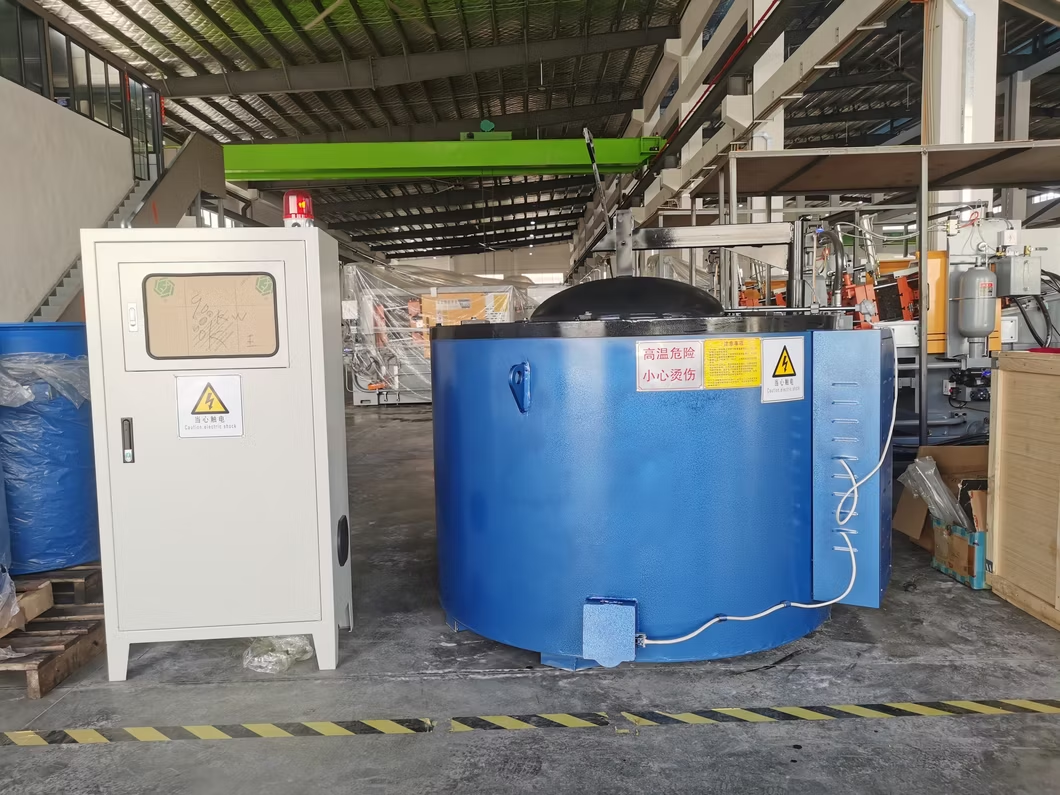
Electric or Nature gas furnace for option.
Easily Operation and Long Service Life.
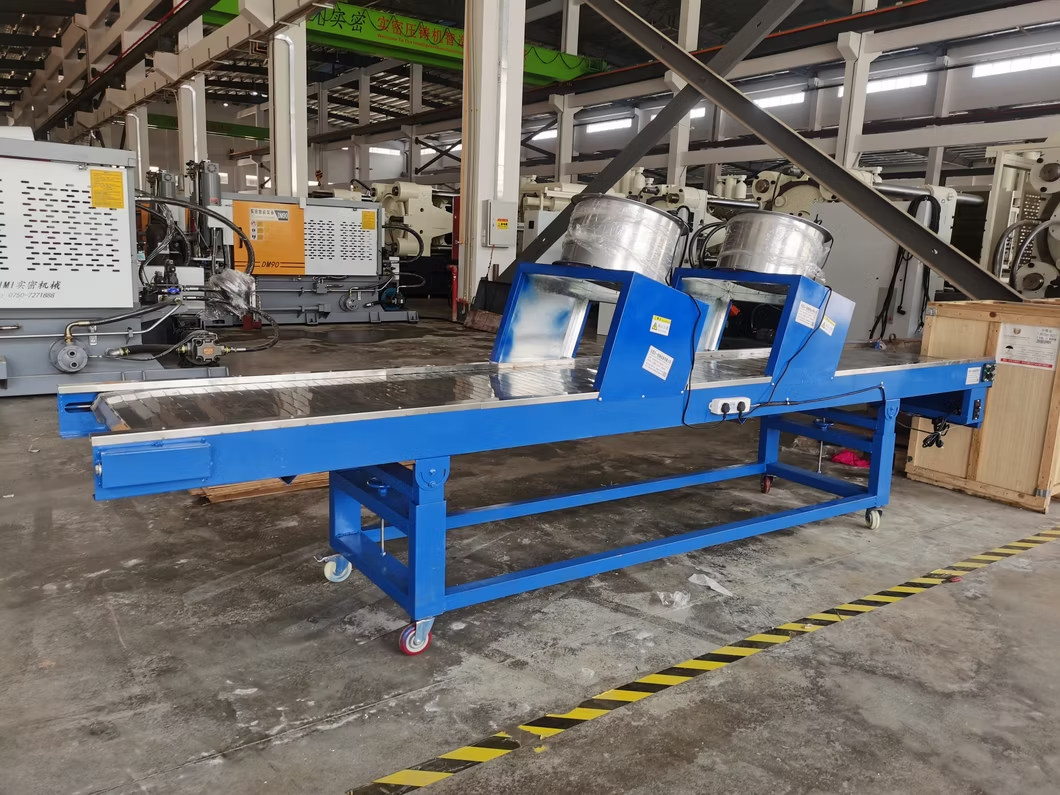
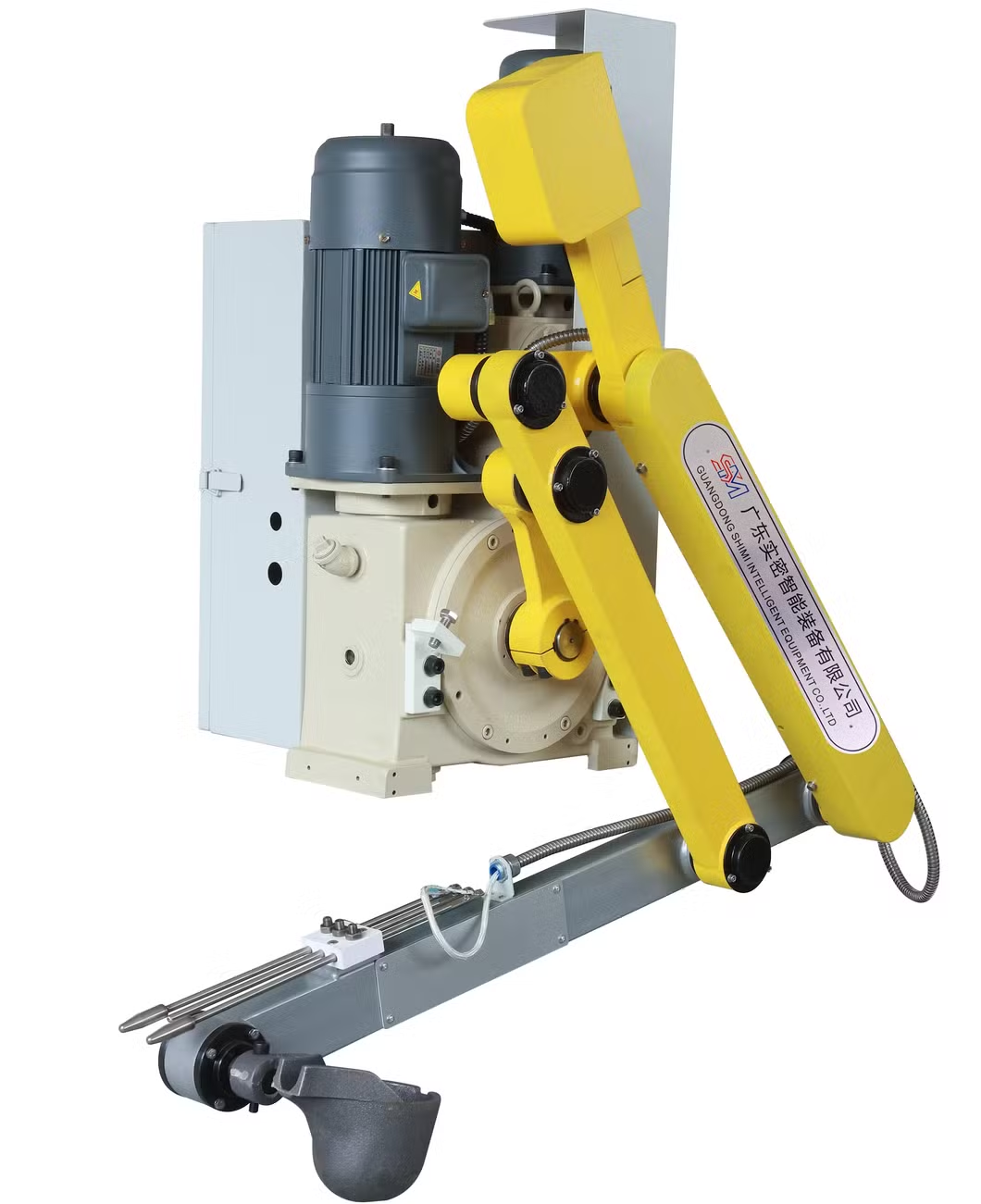
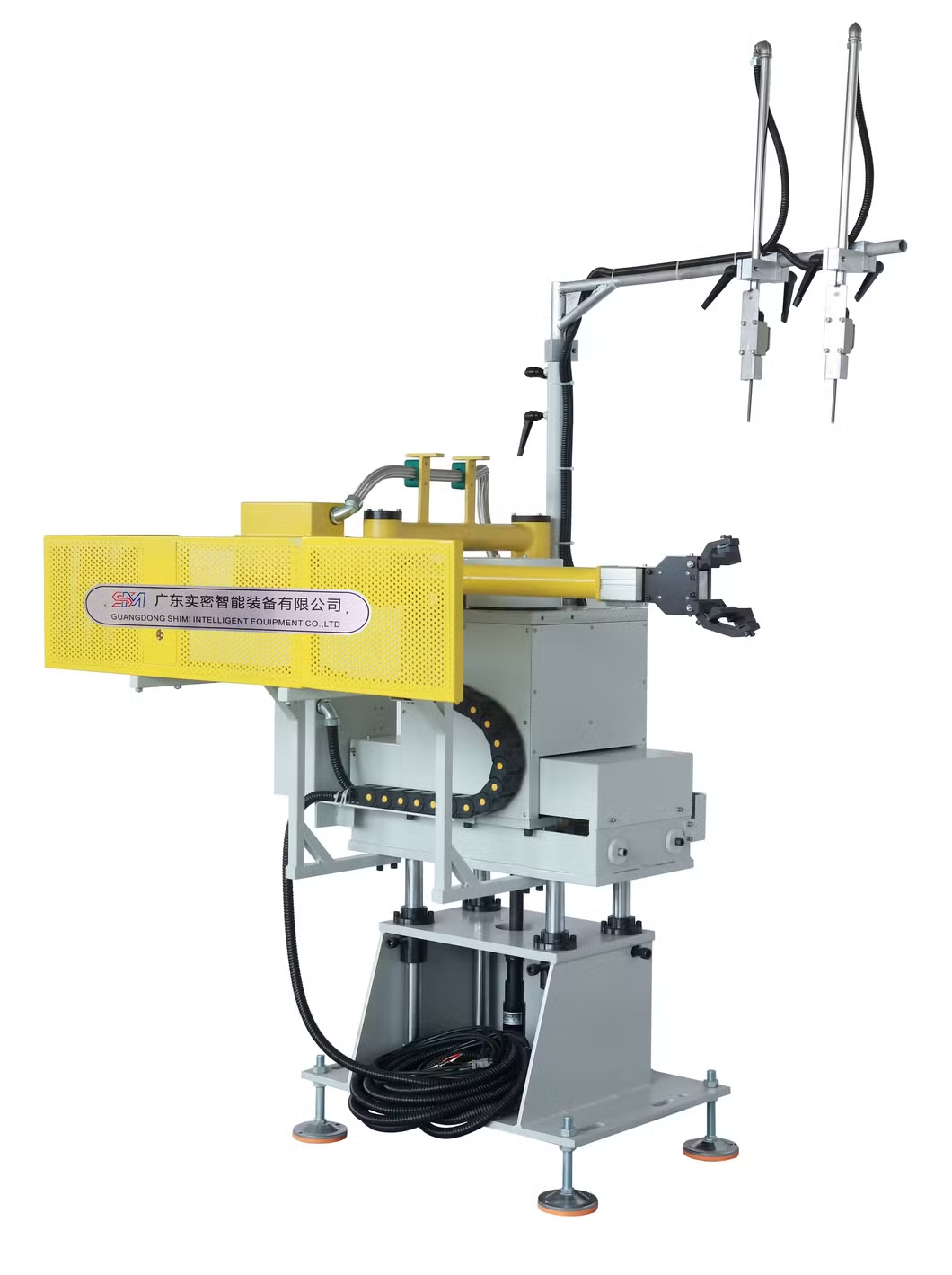
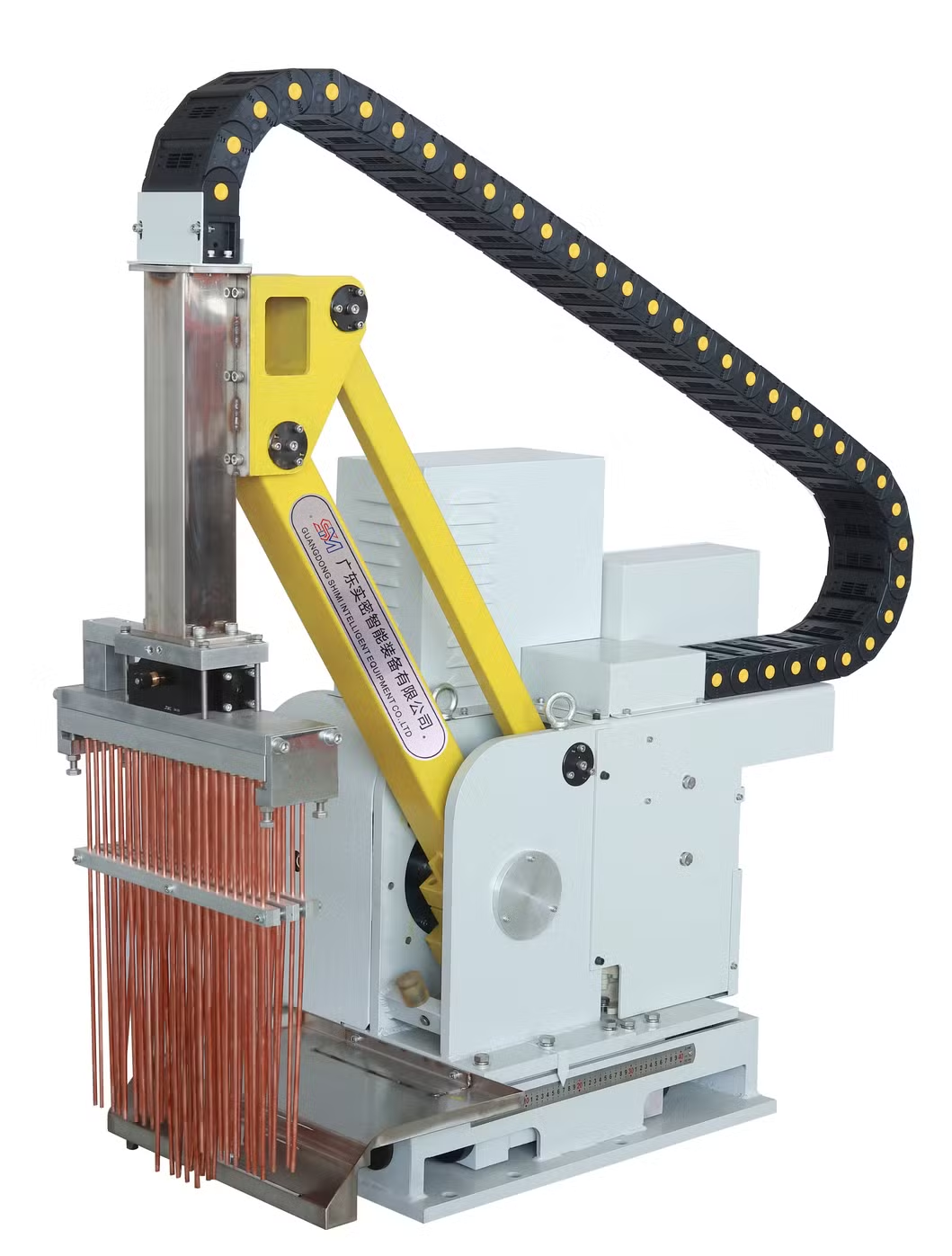
Five Link Automatic Ladle Machine Double-Servo Automatic Extractor Machine Automatic Servo Spraying Machine
Brand List of key Key components :
Item | Brand |
PLC and module | Siemens |
HMI | Siemens |
Frequency converters | Delta |
Encoder | Koyo |
Gearbox | GONGJI |
Servo | Inovance |
ITEM | UNIT | DC 238T |
Clamp Fore | KN | 2380 |
Clamping stroke | MM | 400 |
Ejecting Force | KN | 170 |
Ejection Stroke | MM | 100 |
Mold thickness | MM | 220-670 |
Platen Size (w*h) | MM | 820*820 |
Diameter of die bar | MM | 100 |
Tie bar spacing(w*h) | MM | 530*530 |
Force of shot | KN | 300 |
Stroke of shot | MM | 390 |
Plunger diameter | MM | 50-60-70 |
Shot Weight/Al | KG | 1.42/2.2/2.8 |
Shot Weight/Mg | KG | 0.94/1.47/1.78 |
Casting Pressure (Intensify) | Mpa | 148/104/75 |
Casting area | CM2 | 145/210/284 |
Max Casting area | CM2 | 620 |
Injection Position | MM | 0, - 140 |
Launch distance of shot head | MM | 140 |
Shot chamber flange diameter | MM | 110 |
Shot flange protruding plate height | MM | 10 |
Power of Motor / Servo Motor | KW | 22 |
System working pressure | MPa | 14 |
Oil Tank Volume | L | 600 |
Weight of Machine | KG | 8500 |
Size of Machine | M | 5.6*1.3*2.6 |
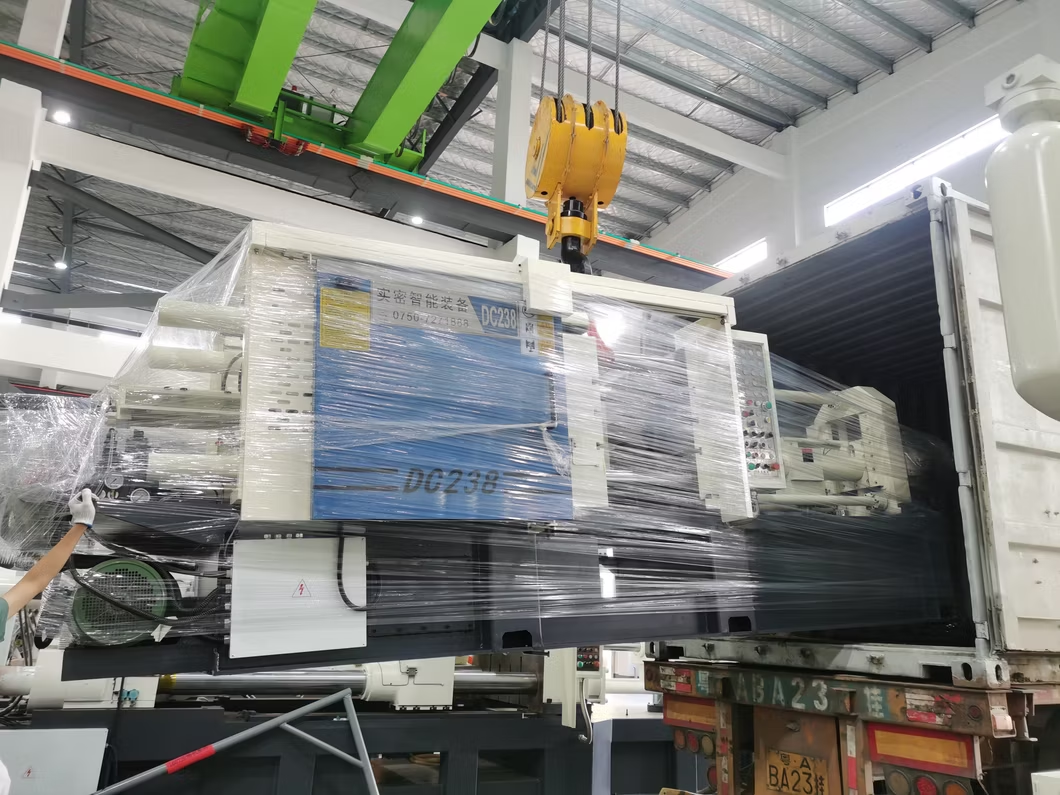
Each of our machines has a final test time over 72 hours before leaving the factory
Ensure that every detail is done to the extreme
On the premise of ensuring the stability and durability of the machine
Create more efficient and energy-saving products
ShiMi die casting machines are widely used to automobile parts, lighting, motor, sport equipment, electric tools, home appliances, bicycles, gas applicances,etc.
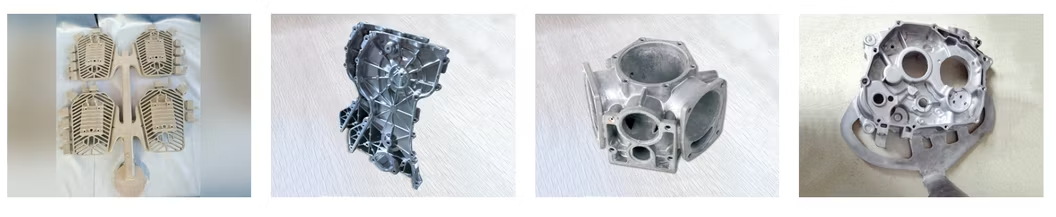

Company Profile
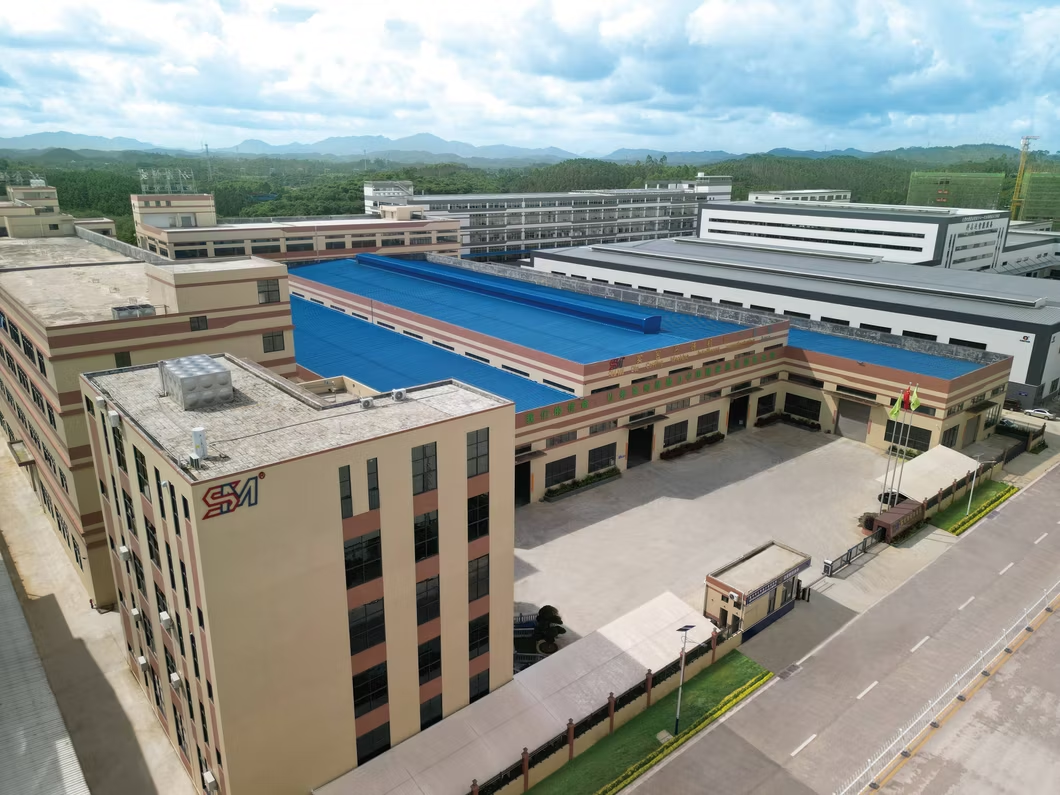
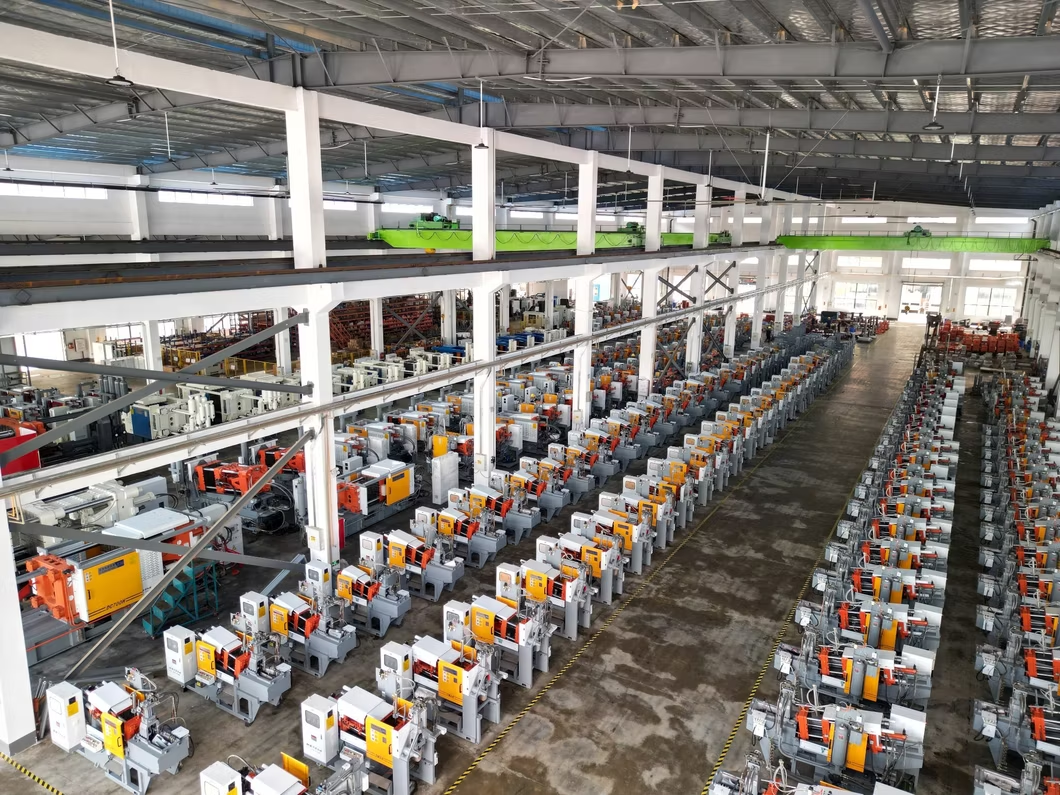
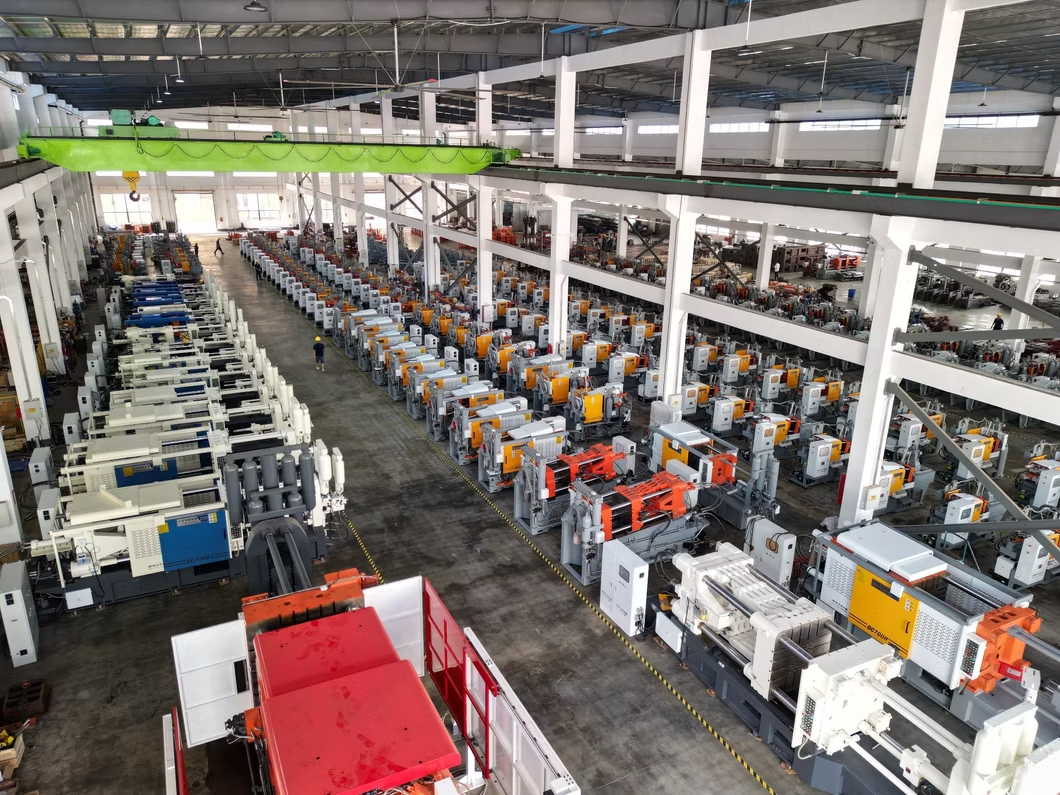
Guangdong Shimi Intelligent Equipment Co., Ltd. is a manufacturing enterprise specializing in R&D, manufacturing, sales and export of cold / hot chamber die-casting machine, vertical die-casting machines and aluminum, magnesium, copper, lead, zinc alloy die-casting machines and semi-solid die-casting machines and extruders, which are widely used in new energy, aviation, auto parts, kitchenware, clothing, lighting, bathroom, hardware and other industries.
Since its establishment in 2009, the company has relied on a professional R&D team, combined with advanced die-casting machine manufacturing technology at home and abroad, independently developed and produced hundreds of reliable products with high performance and high stability, and always walked in the forefront of industry technology, thus realizing the rapid development of the company. and it has invested in a new production base in Enping city ,Guangdong in 2022 , covering an area of 23000 square meters..
The final inspection time of each die casting machine is more than 72 hours before leave factory, to ensure that every detail to be the utmost, to create more efficient, energy-saving die-casting machines under precondition of stability and durability of machines.
We provide customers with one-stop solution for free of charge, from workshop layout, selection of machine models, die design, die casting process, full automatic peripherals to further machining after die-casting .